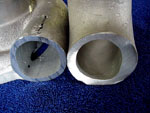
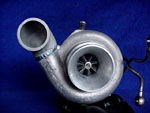 |
Mick
McGreggor Datsun 1600 SR20det
Nervous stuff, putting the saw through a brand new turbo.
Mick became too used to the power of his 12.4 sec. ride, so he has up the
ante with a Garret GT 30bb & associated piping.
There just isn't room to connect a pipe with a good
radius onto the turbo, so we cut the end of the housing off & then welded up
a cast 90 deg. bend to match the shape & contour of the port. Notice
the corresponding "D" shape of the floor of the pipe to the turbo housing.
We also had to make a few templates to make sure we maintained the same
expanding taper in the elbow, which also gave us a better inner radius
ratio. It is important there is no mismatch so close to the turbine
wheel. At least after this the charge has a straight shot at the
intercooler. |
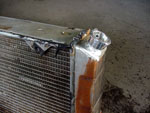 |
Virginia Golf
Club John Deer
We work on almost anything, & this is the slowest so far
(maybe a tie with the pedal car?). The filler kneck had corroded away
(they're only thin stamped alloy oe), so we welded on one of our billet
knecks. Definitely the best part of the cooling system now!
|
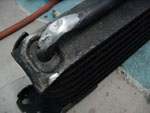
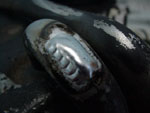
|
Mazbeat of Strathpine had a customer bring in his rotary oil
cooler that had been rubbed through on the bottom pipe
Weld on bottom is normal TIG. weld. We
then changed the
settings on the 'Areowave' & laid the weld down so the repair
was less noticeable when painted.
|
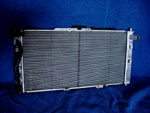
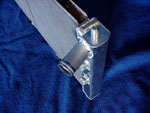
|
Mal Haines
Auto Electrical '93 Maxda Astina import
One of the problems with some (a few) imports
is that parts are not always available locally. A top tank to replace
this cracked one could,'t be sourced anywhere by the owner & is not listed
in any of our catalogues, Neither is an assy., so the only choice was to
fabricated one. Dearer than a tank if it was available, but at least
this tank wont crack.
Fitted straight in. |
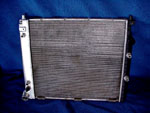
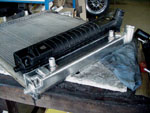
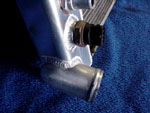
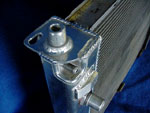
|
RC
Greive Jaguar Jaguar XJ300
This car was involved in an accident & the
bottom of the tank was punched in. No parts are available seperately,
& a new assembly is very expensive. We fabricated a new tank to the
original oe dimentions (except for the oil cooler), turned up a sender
flange & welded it on for approx. 35% of the cost of a new radiator.
Sender flange & Inlet pipe are duplicate of oe. Much
quicker to just cut the back of the pipe off square, but we were asked to
duplicate the plastic tank, & this is a Jag.
It may be easy to manufacture in plastic, but it takes
some time in alloy. At least I know what will last the longest!
|
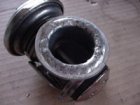
|
Jason May brought this broken HKS blow off valve that came in
on one of his front cuts. We welded abit of scrap on first to get our
settings right & also the correct filler rod.
Welded the flange on to the body & now we have too face it off. We
had to keep the diaphragm wrapped in wet rags or it would've melted.
|
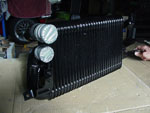
|
Unfortunately I didn't take a pic. of this Supra intercooler before we
started, but this is how it finished up with both pipes being reworked for
an easy fit into a Pulsar ET turbo. Making for a cheap efficient unit,
and easy for the customer to plumb himself.
|
|
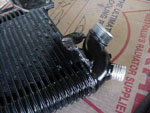 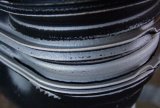 |
Strathpine Toyota had a customer with a leaking GT4 intercooler.
With the size of the split I bet there was
"buggerall" boost in the engine. We have to Hydrogen Braze this type of core
as they are oven fused together in the Denso factory with a lower temp
bonding agent. If we TIG. weld the seam, usually there is a tiny pin hole
leak at the end of the weld because of the higher TIG. welding temperature. |
|
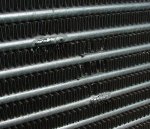
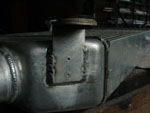 |
Richard Galley dropped in this evo 3 intercooler of his Mit. Gallant rally
car damaged in a minor off. We straightened the damaged fins & then TIG.
welded the two damaged tubes, giving a 100% sound repair. The 'Areowave' was
set to give a high temp surface weld without too much penetration,so that
the fine internal tube fining is not melted. If this happens, they ball up
on the end of the fin & have a slight chance of breaking off. If the ball of
alloy worked it's way down the tube, next stops in the engine!
We also had to weld a pipe onto this end of the tank & pull it back into
shape. It had been punched in & the bracket torn off. We cut the pipe off,
cleaned up the area, straightened the bracket & welded it back on. Pressure
tested to 30 psi. & given back to a relieved owner - for a small fee
offcourse. |
|
|
|
|
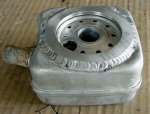
|
A VW Golf oil cooler-filter adapter unit after it had
one hell of a front ender, punching the filter back into the cooler
body
We turned up a new
mount pad & welded it on. It then had to be machined flat to fix a
small distortion We tested the unit for oil-water leaks. |
|
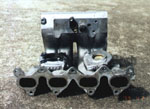
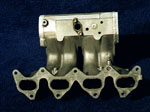
 |
had to have his plenum ends swapped. He was fitting a 4AEG from a
front wheel drive into his KE70 Corolla, which is Rear wheel drive.
This had the throttle body hitting the firewall. It was easier
for us to cut the ends off & throw them as they are not symetrical & so did
not match up at all. Pic. shows the old ends laying in the
runners.
We machined new ends
with identical internal cavities & dimensions & welded them on.
Finished article.
Almost looks factory. |
|
|
Mick McGregors SR20DET throttle body was pointing the wrong way & too
close to mate to the intercooler pipe properly. We had to cut the front off
the plenum on an angle & then machine a thick plate & weld it on |
|
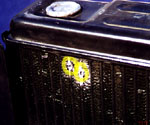
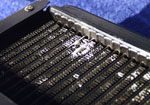
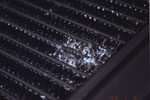
|
This intercooler was damaged when a screw driver slipped, while they
were working on the engine. They thought they would be up for another second
hand unit (they had heard about glue repairs on radiators & didn't want
that) so were really relieved when I said it was no trouble to repair this
properly.
Straight after welding
If the fins weren't
damaged so much, the repair would've been allot better.
|
|